The Ultimate Guide to Hydraulics Pumps
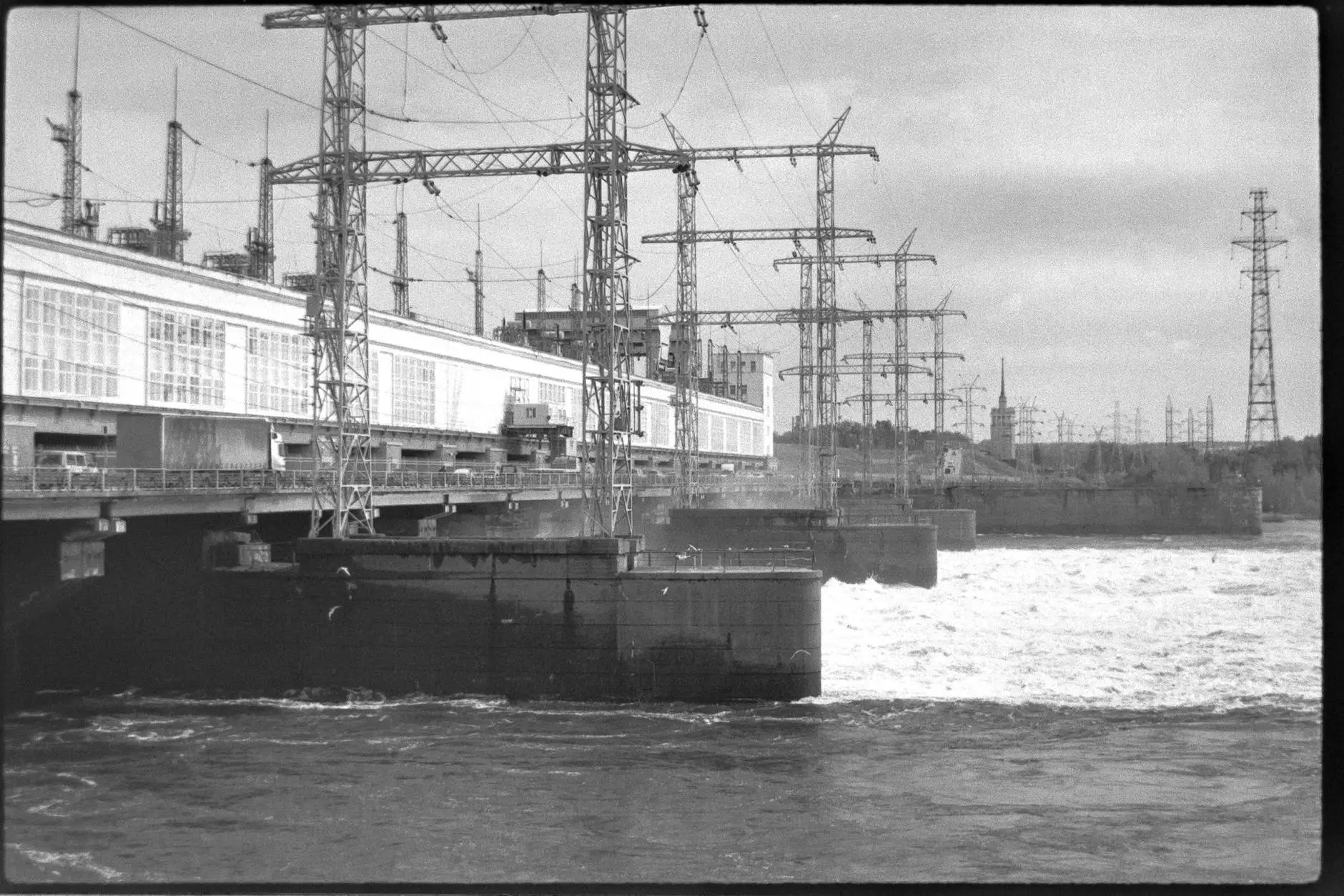
Hydraulics pumps are the backbone of modern machinery, playing a crucial role in various industries, including automotive, construction, and manufacturing. These pumps convert mechanical energy into hydraulic energy, enabling equipment to perform a wide range of functions with remarkable efficiency. In this comprehensive guide, we will delve deeply into the world of hydraulics pumps, exploring their types, applications, benefits, and maintenance practices.
Understanding Hydraulics Pumps
At its core, a hydraulics pump operates by creating flow in a hydraulic system. This flow can lift, move, or control heavy loads with minimal effort. To appreciate their significance, let's break down the fundamental principles of hydraulics:
- Pascal's Principle: This principle states that when pressure is applied to a confined fluid, it is transmitted undiminished in all directions. This allows for the multiplication of force.
- Flow Mechanics: Hydraulics pumps operate by moving incompressible fluids, typically oil, to transmit power through systems, allowing for smooth and controlled operations.
Types of Hydraulics Pumps
Hydraulics pumps come in various types, each designed to cater to specific applications and operational needs. Here are the most commonly used types:
1. Gear Pumps
Gear pumps are among the most widely used hydraulics pumps. Their operation relies on the meshing of gears to create fluid flow. They are known for their simplicity, reliability, and ability to handle a wide range of viscosities.
2. Piston Pumps
Piston pumps utilize cylinders and pistons to transport fluids. They are highly efficient and can achieve high pressure, making them ideal for demanding applications such as construction machinery.
3. Vane Pumps
Vane pumps feature a rotating assembly with sliding vanes. They are known for providing a smooth flow and are often used in medium-pressure applications.
4. Diaphragm Pumps
Diaphragm pumps utilize a flexible diaphragm to move fluids. They are particularly effective for transferring corrosive or viscous fluids, thus expanding their usage across industries.
Applications of Hydraulics Pumps
Hydraulics pumps find applications across numerous sectors, demonstrating their versatility and essential functions:
1. Automotive Industry
In the automotive field, hydraulics pumps are critical in operations such as:
- Power Steering: Power steering systems rely on hydraulics pumps to assist drivers in steering with minimal effort.
- Braking Systems: Hydraulic brake systems use hydraulic pressure to effectively stop vehicles.
2. Motorcycle Parts & Supplies
Motorcycles also benefit significantly from hydraulics pumps:
- Clutch Operation: Many motorcycles use hydraulic clutches for smoother operation.
- Suspension Systems: High-performance motorcycles incorporate hydraulics pumps for adjustable suspension settings.
3. Construction and Heavy Machinery
Hydraulic systems dominate in construction machinery:
- Excavators and Loaders: These machines utilize hydraulics pumps to operate arms, buckets, and other attachments.
- Crane Operations: Hydraulics pumps allow cranes to lift and position significant weights with precision.
Benefits of Using Hydraulics Pumps
There are several reasons why hydraulics pumps are favored in various applications:
- Power Density: Hydraulics pumps can generate large amounts of force in a compact size, making them efficient and effective.
- Control: They provide precise control over speed and torque, allowing for delicate operations.
- Durability: With proper maintenance, hydraulics pumps can last significantly longer than their mechanical counterparts.
- Versatility: Different types of hydraulic pumps can be tailored to fit specific machine needs, whether in vehicles or industrial settings.
Choosing the Right Hydraulics Pump for Your Needs
When selecting a hydraulics pump, it is essential to consider several factors:
1. Application Requirements
Understanding your application's specific demands is crucial. Different pumps have varying maximum pressures, flow rates, and fluid types they can handle, so evaluate what is most important for your use case.
2. Operating Environment
Consider where the pump will operate—indoor, outdoor, or in potentially hazardous environments. This may influence the material and design of the pump needed.
3. Maintenance and Support
Look for pumps that come with easy maintenance guidelines and manufacturer support to ensure longevity and performance optimization.
Maintenance of Hydraulics Pumps
The performance and longevity of hydraulics pumps largely depend on regular maintenance. Here are some practices to consider:
- Fluid Checks: Regularly check hydraulic fluid levels and top-up or change fluids as necessary.
- Leak Inspection: Inspect for any signs of leaks, as they can diminish performance and efficiency.
- Filter Maintenance: Keep filters clean to ensure that contaminants do not enter the hydraulic system.
- Regular Testing: Conduct performance testing to check for any drops in efficiency or operational issues.
Conclusion
In conclusion, hydraulics pumps are an essential component of countless mechanisms that power our world—from automobiles to construction equipment. By understanding the types, applications, benefits, and maintenance of hydraulics pumps, businesses can make more informed decisions that enhance efficiency and productivity.
Whether you are in the automotive industry, a motorcycle enthusiast, or involved in heavy machinery operations, recognizing the impact of hydraulics pumps can lead to better outcomes for your projects. For expert advice, the best hydraulic products, and maintenance tips, visit shophydraulicamerica.com to discover more.