Understanding Die Casting Parts Manufacturers
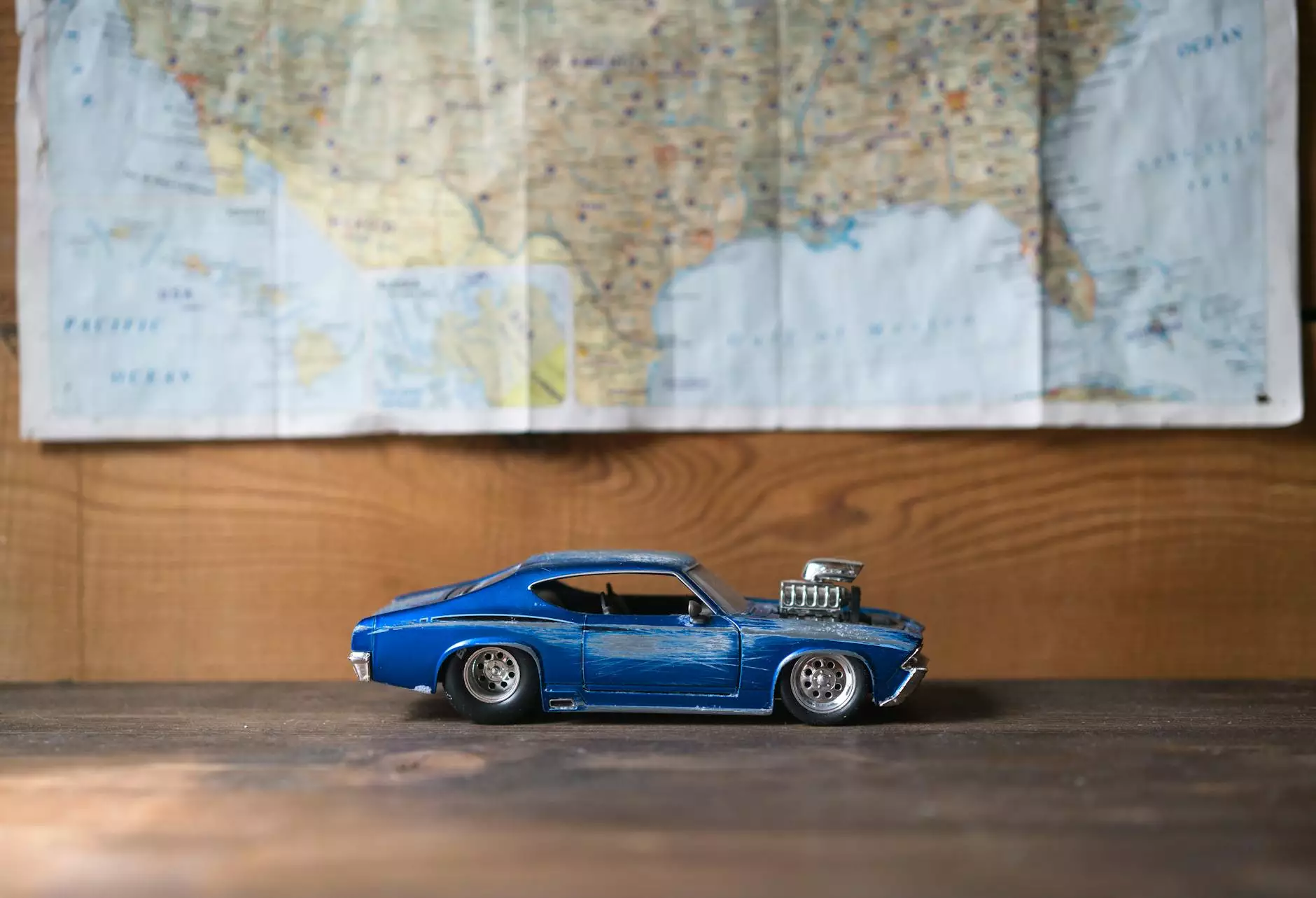
What is Die Casting?
Die casting is a metal casting process that utilizes high pressure to force molten metal into a mold cavity. This innovative process produces parts that are not only accurate but also highly intricate, catering to a plethora of industries such as automotive, aerospace, and consumer electronics.
The Importance of Die Casting Parts Manufacturers
Die casting parts manufacturers play a pivotal role in the production of components that are essential for modern manufacturing. They provide numerous benefits, which include:
- Precision: The high-pressure process ensures tight tolerances and consistency across batches.
- Material Efficiency: Die casting minimizes waste through its accurate molding process.
- Complex Designs: Capable of producing complex shapes that would be challenging to replicate with other manufacturing methods.
- Speed: The ability to produce large volumes of parts quickly significantly reduces lead times.
Types of Die Casting Processes
Die casting is categorized mainly into two types:
1. Hot Chamber Die Casting
In this method, the melting pot is integrated with the die casting machine. It is primarily suited for metals with low melting points, such as zinc and magnesium.
2. Cold Chamber Die Casting
Here, the molten metal is poured into the chamber away from the die casting machine. This method is ideal for metals with higher melting points, including aluminum and brass.
Materials Used in Die Casting
Choosing the right material is crucial for the die casting process. Common materials employed by die casting parts manufacturers include:
- Zinc: Offers excellent corrosion resistance and a smooth surface finish.
- Aluminum: Lightweight, strong, and good for heat conduction.
- Magnesium: Known for its lightweight properties, ideal for reducing overall part weight.
- Copper: Provides high thermal conductivity and an excellent surface finish.
Benefits of Choosing Die Casting Parts Manufacturers
Incorporating die casting into your manufacturing strategy brings multiple advantages:
1. Cost-Effectiveness
Die casting reduces the overall production costs by minimizing material waste, decreasing machining time, and improving production speed.
2. High Durability and Strength
Components produced through die casting exhibit exceptional strength and durability, making them suitable for demanding applications.
3. Enhanced Surface Finish
The process results in a high-quality surface finish, often eliminating the need for additional finishing processes.
4. Design Flexibility
From intricate geometries to complex structures, die casting allows designers to push the boundaries of what's possible.
Applications of Die Casting in Various Industries
Die casting parts manufacturers cater to a wide variety of industries:
1. Automotive Industry
Many automotive components such as engine blocks, transmission cases, and brackets are often fabricated using die casting because of the strength and lightweight nature of the parts.
2. Electronics
The electronics sector utilizes die casting for housings and enclosures, benefiting from the precise dimensions and complex shapes allowed by the process.
3. Aerospace
In aerospace, die casting contributes to the production of precision parts, such as flight control components and structural elements.
4. Medical Devices
Die casting parts manufacturers also serve the medical device industry, creating essential instruments and housings that require strict adherence to standards.
Choosing the Right Die Casting Parts Manufacturer
Selecting a reliable die casting parts manufacturer is crucial for ensuring product quality and meeting deadlines. Here’s a checklist to consider:
- Experience: Look for manufacturers with a proven track record in die casting.
- Quality Certifications: Ensure they adhere to quality standards like ISO 9001.
- Production Capacity: Assess their ability to handle your production volume and timelines.
- Customer Reviews: Check testimonials and case studies for insights into their capability.
The Future of Die Casting
The landscape of die casting is evolving with advancements in technology, leading to:
1. Automation and Robotics
Incorporating robotic systems enhances efficiency and precision in die casting processes.
2. Sustainable Practices
There is a growing trend towards sustainable die casting practices that minimize environmental impact, including better recycling and waste management methods.
3. Advanced Alloys
The development of new alloys and composites is opening doors to stronger and lighter castings.
Conclusion
In summary, die casting parts manufacturers are integral to various industries, providing numerous benefits and applications. By embracing the latest technologies and choosing an experienced manufacturer, businesses can unlock the full potential of die casting to meet their production needs. For businesses looking for top-notch die casting services, exploring options like Deepmould.net can be a game-changer.