Understanding Precision Injection Molds: A Comprehensive Guide
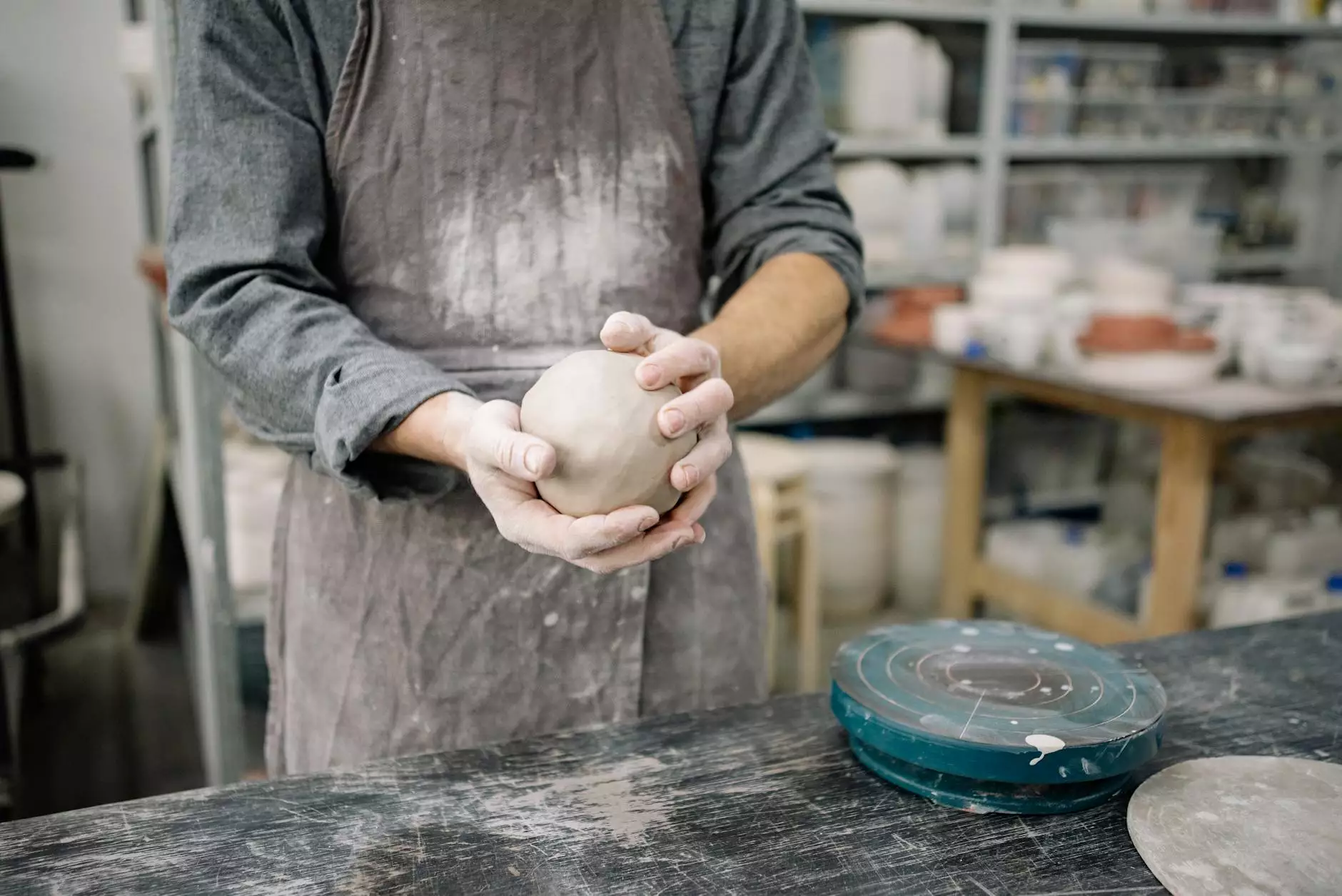
In the world of manufacturing, the term precision injection molds resonates with significance. These molds serve as the backbone of numerous industries, enabling the mass production of intricately designed plastic parts with unparalleled accuracy. In this article, we will delve deep into the intricacies of precision injection molds, covering their importance, design processes, applications, and the benefits they bring to various sectors.
What are Precision Injection Molds?
Precision injection molds are specialized tools used to create parts by injecting molten material into a mold cavity. This process is instrumental in producing a wide range of products, from consumer goods to automotive components. The precision aspect relates to the exactness with which these molds are designed and manufactured, ensuring that every part produced meets the specified dimensions and tolerances.
The Importance of Precision in Injection Molding
Precision in injection molding is critical for several reasons:
- Quality Control: High precision leads to consistent quality in the final products, reducing the likelihood of defects.
- Cost Efficiency: Accurate molds reduce waste and rework, lowering production costs.
- Material Optimization: Better precision allows for the use of materials more effectively, enhancing product durability.
- Time Savings: Precise molds shorten production times, allowing companies to meet demands swiftly.
The Design Process of Precision Injection Molds
Designing precision injection molds is a meticulous process that involves several steps:
1. Conceptualization
Every project starts with a concept. Designers collaborate with engineers and clients to understand the intended use of the product and its specifications. This stage often involves sketching preliminary designs and exploring possible materials.
2. CAD Modeling
Once the initial design is approved, engineers use Computer-Aided Design (CAD) software to create detailed 3D models of the molds. This technology allows for intricate designs that ensure optimal performance of the molds.
3. Mold Flow Analysis
Before manufacturing the molds, it is essential to simulate how the molten material will flow within the mold. Mold flow analysis helps identify potential problems, such as air bubbles and insufficient filling, ensuring that the final product meets quality standards.
4. Manufacturing
After validation, the actual mold is manufactured. This step typically involves high-precision machining techniques, such as CNC milling and electrical discharge machining (EDM), which create the mold components with exact specifications.
5. Assembly and Testing
Once all parts are machined, they are assembled and rigorously tested. Quality checks ensure that the molds function correctly and produce the intended parts without any issues.
Applications of Precision Injection Molds
Precision injection molds find applications across various industries, underscoring their versatility and importance. Some key sectors include:
1. Automotive Industry
The automotive sector relies heavily on precision injection molds for creating intricate components such as dashboards, bumpers, and interior fittings. The high level of accuracy ensures that these parts function correctly and fit seamlessly in vehicles.
2. Consumer Electronics
From smartphone cases to intricate circuit boards, consumer electronics depend on precision molds to create lightweight yet durable components. The demand for sleek designs with high functionality drives the need for precision in this sector.
3. Medical Devices
In the medical field, precision is paramount. Medical devices such as syringes, drug delivery systems, and diagnostic equipment require parts that meet stringent regulatory standards, making precision injection molds crucial for their production.
4. Packaging
Additional advancements in packaging, such as single-use bottles and containers, utilize injection-molded components. Precision molds ensure uniformity and reliability in packaging solutions.
Advantages of Using Precision Injection Molds
Investing in precision injection molds offers several advantages, making them a preferred choice for manufacturers:
- Enhanced Production Speed: Precision molds enable rapid production cycles, which is essential in meeting market demands.
- High Durability: Well-constructed molds offer longevity, reducing downtime and maintenance costs.
- Scalability: Precision molds can easily adapt to produce varying quantities, catering to both small and large-scale production.
- Design Flexibility: Advanced molds allow for complex designs that were previously unattainable with traditional methods.
Challenges in Precision Injection Molding
Despite the numerous benefits of precision injection molds, several challenges can affect the process:
1. High Initial Investment
Creating precision molds often requires significant upfront capital. The costs associated with high-quality materials and advanced machining processes can be a barrier, especially for small businesses.
2. Technical Expertise
The design and manufacturing of precision molds demand a high level of technical expertise. Lack of skilled personnel can hinder the production process and affect the quality of the final products.
3. Maintenance and Repair
While precision molds are durable, they still require regular maintenance. Implementing a proactive maintenance plan is crucial to avoid downtime and unexpected costs.
Future Trends in Precision Injection Molding
The world of manufacturing is constantly evolving, with several trends likely to shape the future of precision injection molds:
1. Technological Advancements
With advancements in technology, we can expect better materials, improved CAD software, and enhanced manufacturing processes. These innovations will further refine the precision of molds and the efficiency of production.
2. Sustainability Efforts
As industries move towards eco-friendliness, the development of precision injection molds that utilize recycled materials and consume less energy will become more prominent.
3. Integration of Automation
Automation in the manufacturing process will increase, enhancing the speed and accuracy of mold production while reducing labor costs and human error.
Conclusion
In conclusion, precision injection molds are integral to the manufacturing process across various sectors, ensuring high-quality, consistent, and cost-effective production. By understanding the design, applications, advantages, and challenges of these molds, businesses can make informed decisions on their manufacturing processes. The future of precision injection molding looks bright, with ongoing advancements promising even greater efficiency and sustainability. As industries continue to evolve, the role of precision injection molds will only become more critical in shaping the products of tomorrow.
For businesses looking to enhance their manufacturing capabilities, investing in precision injection molds is not merely an option; it is an essential strategy for staying competitive in a fast-paced market. To explore more about precision injection molding and how it can benefit your business, visit deepmould.net.