The Importance of Choosing the Right Plastic Injection Mould Manufacturer
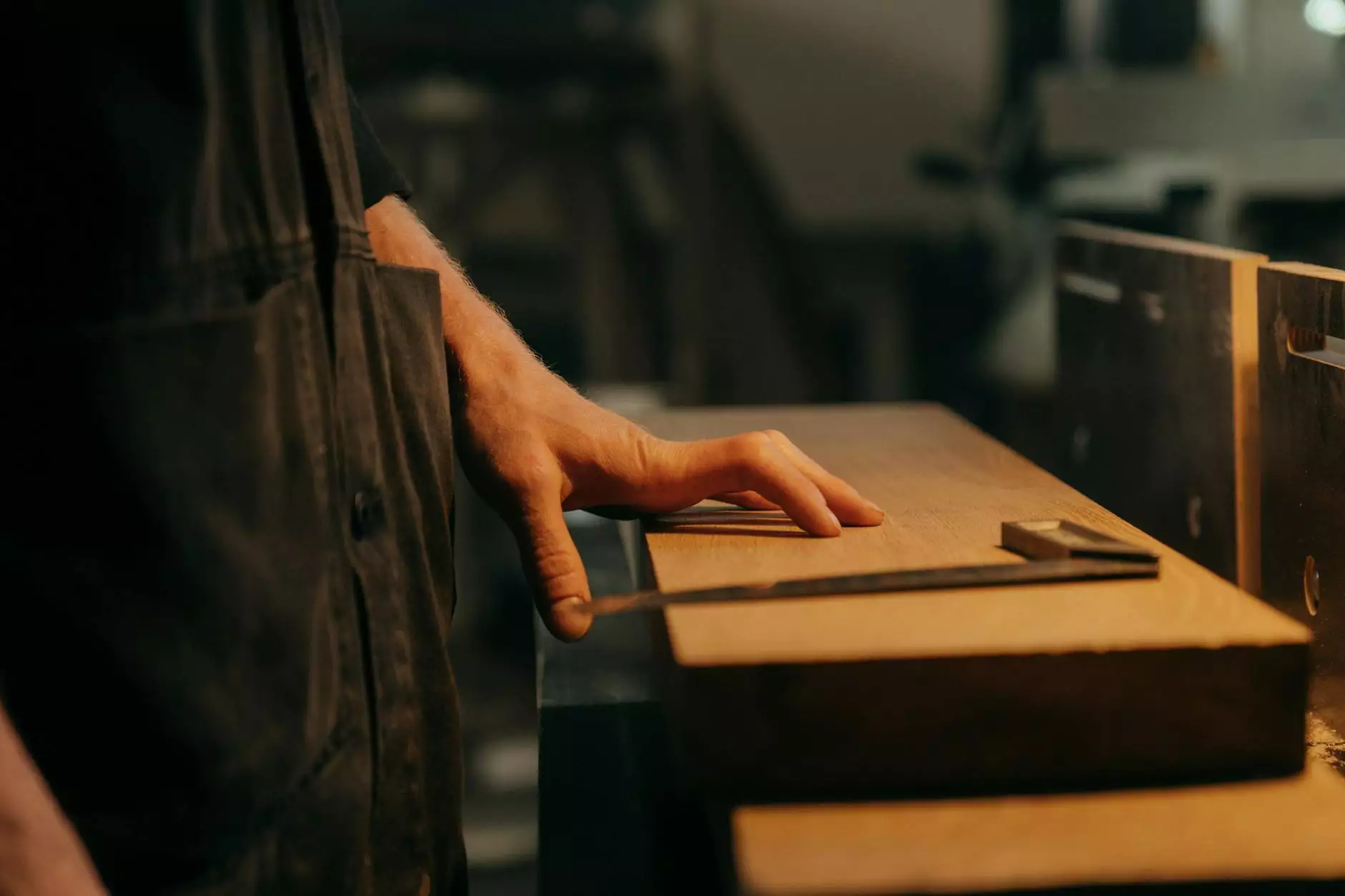
In today's fast-paced manufacturing world, the choice of a plastic injection mould manufacturer can significantly impact the success of your product development process. With the growing demand for precision-engineered plastic components across various industries, selecting a reliable manufacturer who understands the intricacies of injection moulding is essential for achieving high-quality results that meet your specifications and timelines.
What Is Plastic Injection Moulding?
Plastic injection moulding is a manufacturing process used to create parts by injecting molten plastic into a mould. This technique is known for its efficiency, precision, and ability to produce complex shapes in high volumes. It involves several steps, including:
- Material Selection: Choosing the right type of plastic for the intended use of the final product.
- Mould Design: Engineering a mould that can produce the desired shape while accommodating the properties of the selected plastic.
- Injection Process: Heating the plastic to a molten state and injecting it into the mould under high pressure.
- Cooling and Ejection: Allowing the moulded part to cool and then ejecting it from the mould.
Why Choose a Reliable Plastic Injection Mould Manufacturer?
When selecting a plastic injection mould manufacturer, there are several key factors to consider. The right choice can lead to enhanced product quality, reduced costs, and quicker time-to-market. Here are some compelling reasons to prioritize quality in your selection:
1. Quality Assurance
A reputable plastic injection mould manufacturer places significant emphasis on quality control. They possess the right certifications and adhere to industry standards, ensuring that every product produced meets high-quality benchmarks. This commitment to excellence translates into:
- Consistent Product Performance: Reducing defects and improving the longevity of the products.
- Enhanced Safety: Meeting regulatory requirements for various industries, such as healthcare and automotive.
- Client Satisfaction: Building trust through reliable and high-quality output.
2. Cost Efficiency
Working with experienced manufacturers can also lead to cost savings in the long run. An expert plastic injection mould manufacturer can help optimize the production process, which can include:
- Material Optimization: Suggesting the best materials for cost-effectiveness while ensuring product quality.
- Streamlined Processes: Implementing advanced manufacturing techniques that reduce waste and save time.
- Volume Production Discounts: Offering better pricing for bulk orders which can significantly lower per-unit costs.
3. Advanced Technology
Today’s leading plastic injection mould manufacturers invest in cutting-edge technology that enhances production capabilities. This might include:
- 3D Printing Technology: Allowing for rapid prototyping and quicker turnaround times for initial designs.
- Computer-Aided Design (CAD): Utilizing software to ensure precision in mould design and development.
- Automation: Implementing robotic systems for increased efficiency and reduced human error.
Choosing the Right Plastic Injection Mould Manufacturer: Key Considerations
With a plethora of options available, here are the essential considerations when selecting a plastic injection mould manufacturer that aligns with your business goals:
1. Experience and Expertise
Choose a manufacturer who has extensive experience in the industry. A long-standing background usually indicates a deep understanding of the injection moulding process and the challenges that might arise. Ask about their previous projects and industries they serve to gauge their versatility and expertise.
2. Customized Solutions
Every business is unique, with specific needs and requirements. The ability to offer customized solutions tailored to your specifications is an essential feature of a top-tier plastic injection mould manufacturer. This includes discussions on:
- Tailored mould designs that meet specific dimensional and functional requirements.
- Adaptation of production processes based on unique materials and product designs.
- Support in the entire development cycle, from design to final manufacturing.
3. Customer Support and Communication
Strong communication is vital for a successful partnership. Assess the level of customer support offered by the manufacturer, including:
- Responsiveness: Quick replies to inquiries can indicate their overall service commitment.
- Project Management: Clear processes for updates and feedback throughout the production timeline.
- Technical Support: Availability of engineering support when needed for troubleshooting or design enhancements.
Emerging Trends in Plastic Injection Moulding
The landscape of plastic injection moulding is continually evolving, influenced by technological advancements and market needs. Here are some trending areas that may shape the future of this industry:
1. Sustainability in Materials
As global awareness of environmental issues grows, many manufacturers are now focusing on sustainable practices. This includes:
- Incorporating recycled materials into the injection moulding process.
- Developing biodegradable plastics that minimize environmental impact.
- Implementing processes that reduce energy consumption during production.
2. Smart Manufacturing
Industry 4.0 principles are making their mark in plastic injection moulding through:
- IoT technologies that enable real-time monitoring and data analysis.
- Smart moulds that can provide feedback and optimize production in real-time.
- Predictive maintenance that helps avoid equipment downtime.
3. Advanced Biocompatible Plastics
Demand for biocompatible plastics is on the rise, particularly in the medical field. Manufacturers are starting to:
- Research and develop new materials that are safe for use in medical devices.
- Focus on processing techniques that maintain the integrity of these sensitive materials.
Conclusion
The selection of a skilled and experienced plastic injection mould manufacturer can serve as a crucial factor in your production success. By understanding the complexities and benefits associated with this manufacturing process, businesses can ensure they are making informed choices that lead to better products, improved efficiency, and ultimately, greater market competitiveness.
Hanking Mould, with its commitment to quality, customization, and state-of-the-art technology, stands ready to support your injection moulding needs. By partnering with such a manufacturer, you are not only investing in superior products but also paving the way for innovative future solutions.